Engineering
mass production and satisfy customer requirements.
ALTEN KOREA is developing and using advanced designs and verification procedures that utilize VR systems.
Engineering Process
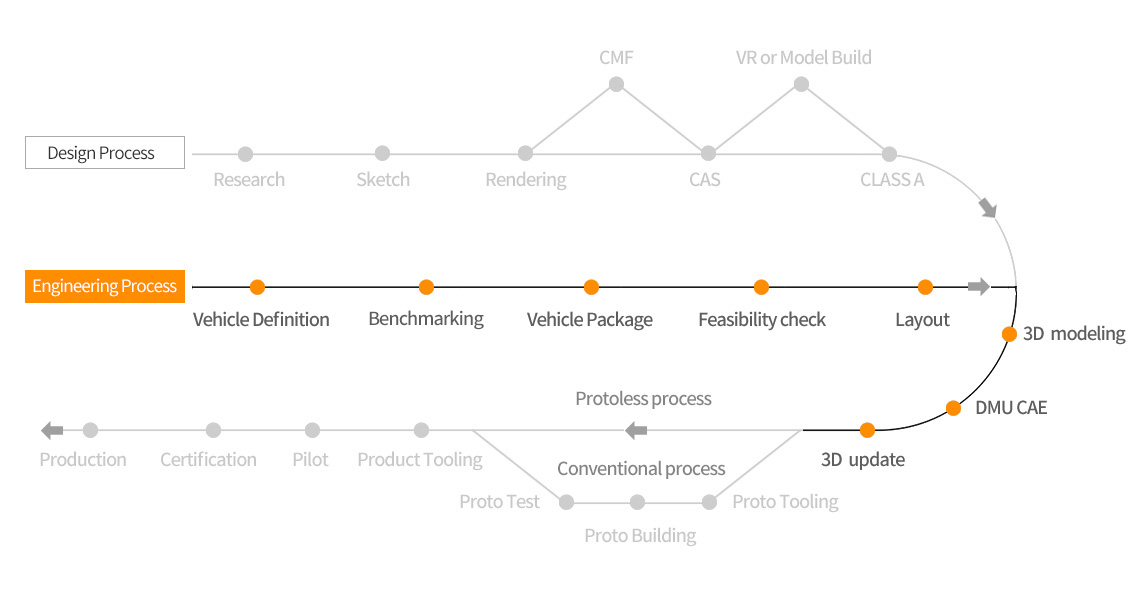
Step 01. Vehicle Definition
Establish directions and product concept for new car development
- Segment
- Body Style (N/B, H/B, SUV…)
- 2WD/AWD/FWD
- Initial Dimension
- Implementation plans for key systems (P/T, Chassis…)
- New System implementation plan
Design Image development
- Idea Sketch
Establishment of development objectives
- Target Markets
- Safety Targets
- Performance Targets
- Mass & Cost Targets
- Target SOP Timing
Step 02. Benchmarking
Reference & Completive Car Tear-down Analysis
- Design Analysis
- Mass & cost Analysis
- Highlight Item Analysis
- Manufacturing Engineering Analysis
- BIW Bending/Torsion Test & Modal Test
- Typical Section
Virtual Benchmarking
- 3D Scanning & Digitizing
- 3D Motion / Analysis
- Package & Layout Analysis
- Key System analysis
Step03. Vehicle Package
Initial Package Drawing
- Vehicle Key Dimensions
- Occupant Positioning & Packaging
- Coarse Sections Study
- GA Drawing Release & Up date
System Lay-out configuration
- Carry-over Apply System Review
- New Major System Selection and System Integration
Concept Section
- Suggest Reference : Master section
- Engineering Feasibility check
Step 04. Feasibility Study
Legal Feasibility
- Review of related legislation in country of sale ex.) Pedestrian Protection
Market/Planing Feasibility
- customer and market requirements, and product planning requirements ex.) Market Analysis, VOC
Engineering Feasibility
- Verification of customer and in-house design requirements
- Package confirmation that review feedback is reflected in final design
- Confirmation of satisfaction of mass production requirements and gap/offset conditions ex.) Approach Angle
Manufacturing Feasibility
- Confirmation that mass production requirements are satisfied
- Confirmation that mass-production component supplier/tooling vendor requirements are satisfied, e.g., Side Outer Draw Depth
Step 05. Layout
Engineering Requirments
- Package Requirements
- System Lay-Out
- New PT installation Requirements
- Design specification Concept, construction method, performance determination
- Mass , Cost Targe
Market Requirements
- Domestic and overseas customer requirements and trends
- NCAP requirements according to area of export
- Requirements for improvement of currently produced vehicles
Legal Requirements
- Collision safety laws in each country (head-on collision, side collision, pedestrian safety-related laws, etc.)
- Environmental regulations for emissions gases and noise
- Verification of potential to meet regulations relating to the recovery of recyclables
Manufacturing Requirements
- Conformance with in-house mass production requirements
- Due consideration of processes/methods of key suppliers
- Reflection of work environment improvement requirements, including work posture
Step 06. 3D Modeling
Initial skin data, master section and initial package drawing used to prepare system 3D data to meet market, engineering, legal and mounting requirements
Preparation of 3D data with consideration of gaps/offsets
CAS and Class-A surface data finalization followed by 3D data update
3D data reviewed based on client-designated tooling maker and specifications prior to distribution
Basic data for CAE analysis
Step 07. DMU CAE
Verified using virtual simulation for shorter development period and cost savings
- Crashworthiness
- DMU
- FMH
- Pedestrian protection
- Luggage Intrusion Analysis
- Structural Stiffness Analysis
- CFD Analysis
Verification using DMU (Digital Mock Up)
- Design quality verification and component clearance/interference check
- Early verification of assembly performance, workability and ease of maintenance
Step 08. 3D update
Client requirements
- Reflect requirements such as design concept, target weight, and performance.
Legal and NCAP Follow-up
- Market requirements review and design reflection
Performance
- Performance verification and design reflection through CAE
Manufacturing
- Mass production verification and design reflection through SE
Design Optimization
- Design Review and Design Optimize using ALTEN KOREA Deep Process
